A new waterjet cutting machine at Sectomo
We have some exciting news to share with you, straight from our factory, Sectomo. A new waterjet cutting machine has arrived and is now in use. This is our biggest purchase since the production was moved to our own hands in 2017. With our very own waterjet cutting machine we will be able to ensure better quality, reliability of delivery and greater flexibility.
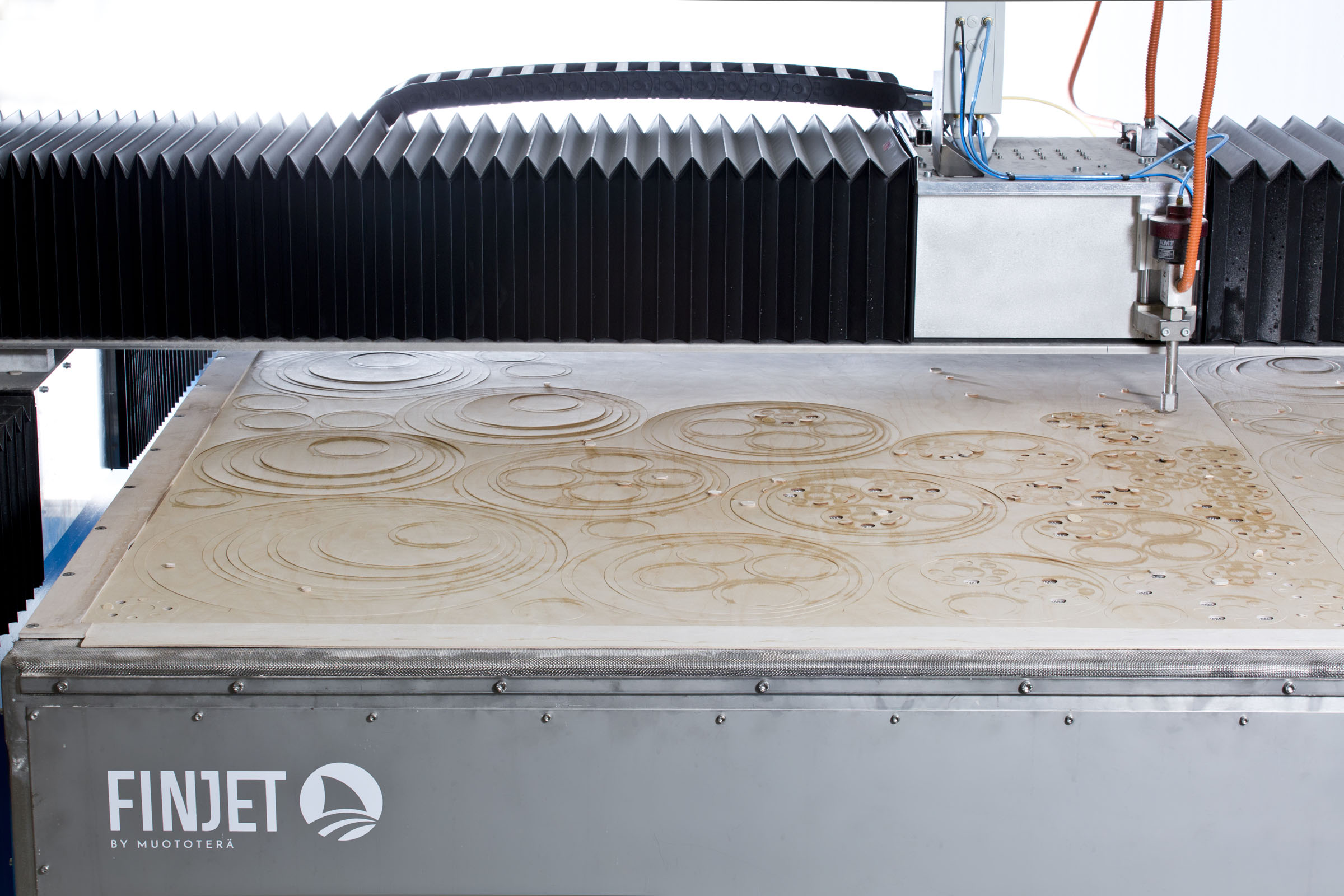
The FinJet waterjet cutting machine by Muototerä, a Tampere based family run company, is also made in Finland. Photo by Uzi Varon.
As a Finnish company to whom local production is an important value, it also felt meaningful to select a waterjet cutting machine that is made in Finland. We chose the FinJet waterjet cutting machine by Muototerä, a Tampere based family run company. They have been manufacturing the water cutting machines since 1987 – from the times these kinds of machines were still brand new technology in Europe. FinJet waterjet cutting machine turns water into an environmentally friendly, efficient and accurate cutting method.
We are happy for this purchase as we are now able to produce the rings, that are the essential cohesive elements of the Secto Design lamps, at our own premises. The water cutting machine is mainly used for cutting the rings, but will also be used for making our own tools and utensils. From now on, we can also utilize the leftover pieces of thin veneer in our own production or they can be benefited at the hands of another producer of wood products. This equals to a minimum amount of loss, which is highly important to a company emphasizing sustainability as one of it’s key values. Waterjet cutting is a sustainable choice, as there are no toxics used in the process of cutting or harmful by-products caused by it. We use only pure water when we cut our rings. Also the resulting surface remains natural thanks to watercutting, that doesn't cause any burning marks.
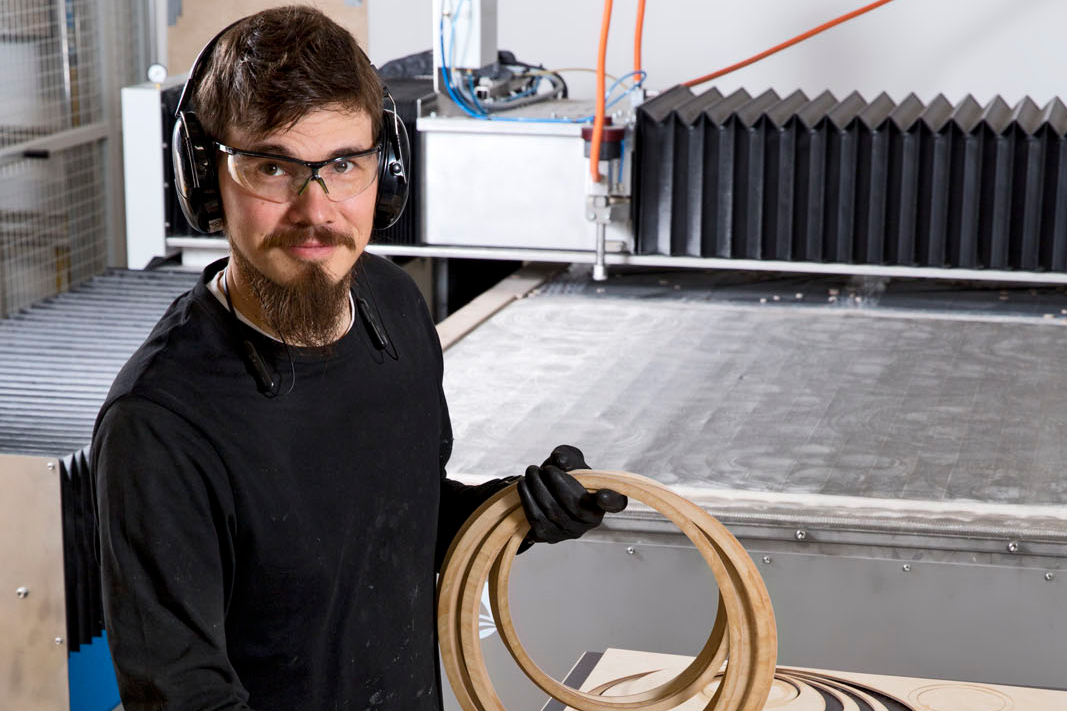
Tapio Kangasniemi, in charge of Production Development at Sectomo is excited to have the new waterjet cutting machine in the house! Photo by Uzi Varon.
We had a chat with Tapio Kangasniemi who’s in charge of the Production Development at Sectomo to find out more about the process of waterjet cutting.
1. What is waterjet cutting?
Waterjet cutting machine is an industrial tool capable of cutting a wide variety of materials using a very high-pressure jet of water. Basically waterjet cutting machine is using high pressure water focused into a beam by a tiny nozzle making it possible to cut through an object.
2. What are the advantages of cutting when comparing with traditional methods of working the wood?
The advantage of waterjet cutting when compared with the more traditional CNC working is that in CNC cutting the amount of the material being removed is high, unlike in waterjet cutting where we don’t end up having much waste generated from tools.
In addition, the water doesn’t burn as let’s say laser does. Also the costs of tools are a lot smaller as the waterjet cutting machine itself doesn’t really wear out and here in Finland there is enough water available. In addition, the way of working is different with the water jet cutting machine and it enables diverse working. In the waterjet cutting the high pressured jet of water is very thin, the nozzle in use very small resulting to also a very thin water jet. In our case, we cut birch plywood, with fresh high pressure water. We use the pressure of 4000 bars.
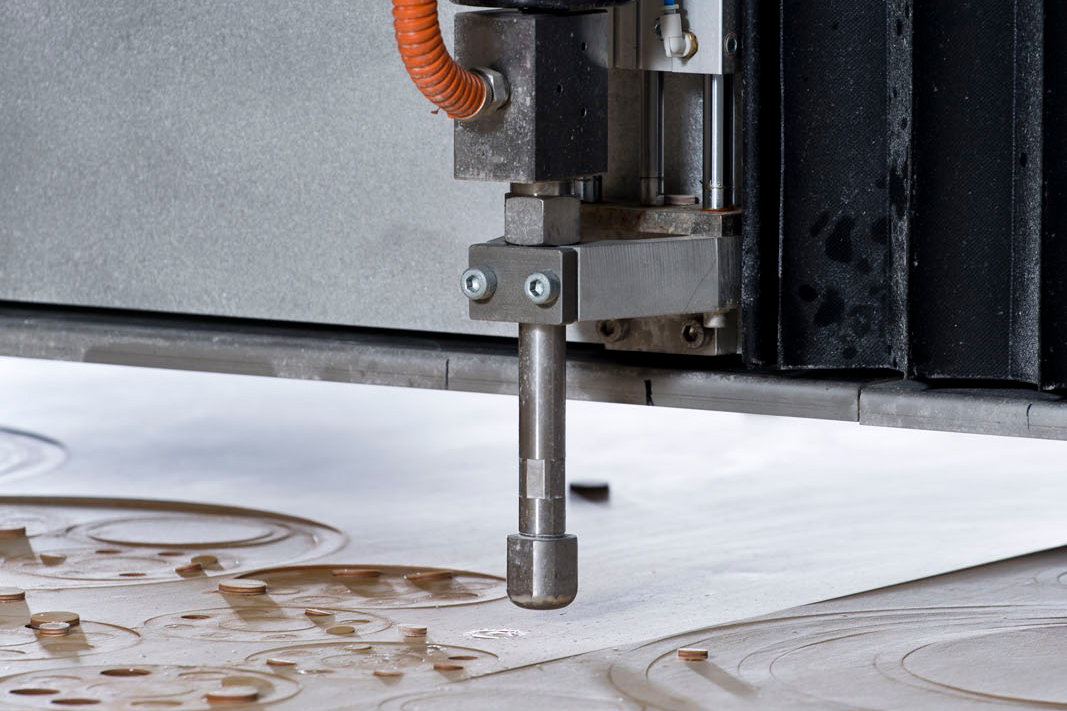
Waterjet cutting machine is an industrial tool capable of cutting a wide variety of materials using a very high-pressure jet of water. Photo by Uzi Varon.
3. What can be cut with waterjet cutting machine?
The options are almost unlimited!
Waterjet cutting can be used for almost all materials. It covers also
materials that cannot withstand heat. When cutting with pure fresh
water, also the material being worked has to be porous enough. This
means the plywood we cut is an ideal material for waterjet cutting.
In general, the same cutting method is also widely being used in a
grocery field. Cutting cakes and cheeses with the high pressure jet
of water is precise and hygienic! If fine abrasive substance is added
to the waterjet, cutting almost anything at all is possible!
Traditionally in the waterjet cutting there is also fine abrasive
substance being mixed with water in order to be able to cut even
stronger materials, such as steel, aluminum or even stone.
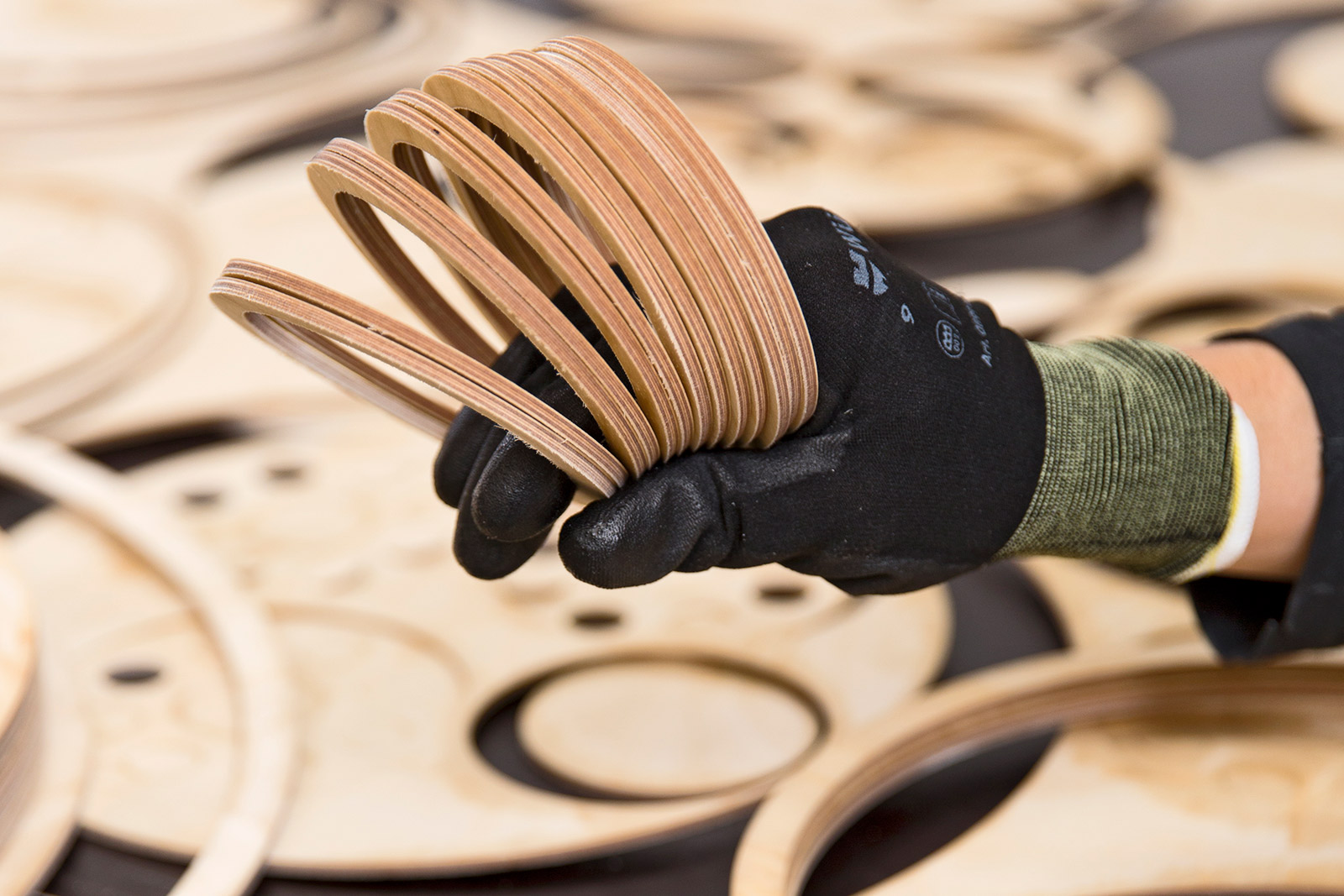
We are now able to produce the rings, that are the essential cohesive elements of the Secto Design lamps, at our own premises. Photo by Uzi Varon.
We are excited to have our FinJet waterjet cutting machine in the house and look forward to all the possibilities it brings with it. Who knows, maybe one can see the results in the future Secto Design models! Time will tell.